DLG-NC401 Automatic screw welding machine
Working process
(1) Arc generation
There are two kinds of arc generating devices inside the equipment, which supply non transfer arc and transfer arc respectively.The negative electrodes of the two power supplies are connected in parallel and connected to the tungsten electrode (negative electrode) of the stack welding gun through a cable.The positive pole of the non transfer arc power supply is connected to the nozzle of the stack welding gun through the cable, and the positive pole of the transfer arc power supply is connected to the workpiece through the cable.The cooling water is led to the welding gun through the water-cooled cable to cool the nozzle and electrode.Argon enters the welding torch through solenoid valve and rotameter.After the power is turned on, the non transfer arc is ignited by high frequency spark.Then the transfer arc is ignited by the conductive channel between the tungsten electrode and the workpiece caused by the non transfer arc flame.After the transfer arc is ignited, the non transfer arc can be retained or cut off.It mainly uses transfer arc to produce molten pool on the surface of workpiece.
(2) Solder powder output
The alloy powder is continuously supplied by the powder feeder according to the demand, and is sent into the welding gun with the aid of powder feeding gas (generally argon) and blown into the arc.The alloy powder is heated in advance in the arc column, in a molten or semi molten state, and sprayed into the molten pool of the workpiece, where it is fully melted, and the gas and slag are discharged.
(3) Parameter adjustment
By adjusting the transfer arc and non transfer arc current, powder feeding amount and other process parameters, the heat transferred to the workpiece and melted alloy powder can be controlled.With the relative movement of the welding gun and the workpiece, the alloy pool gradually solidifies and the required alloy deposit layer is obtained on the workpiece.
Characteristics
Compared with other surfacing methods, plasma surfacing has many advantages because it uses plasma arc as heat source and alloy powder as filler metal.
(1) High cladding speed and high productivity.
(2) The penetration is controllable and the dilution rate is low.
(3) The surfacing surface is flat and smooth with high density, and the surfacing surface of 0.5-5mm can be completed at one time.
(4) The stable surfacing layer can be obtained continuously for a long time, and the surfacing surface has no quality problems such as porosity and trachoma.
(5) The alloy powder is easy to prepare and can be used in a wide range of materials. Cobalt based, nickel based, iron-based and copper based powder welding materials can be selected, and the formula can be directly formulated according to the working conditions.
(6) It can be equipped with special machine, robot, etc. according to the demand, which is easy to realize automation and reduce labor intensity.
(7) The utilization rate of powder is high, and the utilization rate can reach more than 75%.
Overview
Screw as the core part of plastic machinery, its life is very limited, it is a vulnerable spare parts.In the industry application, in order to improve production efficiency, reduce equipment downtime maintenance and so on.Therefore, the surface strengthening treatment (wear resistance, high temperature resistance and corrosion resistance) of the screw is realized by plasma surfacing, so as to meet the requirements of working conditions.
Material
More than 90% of the plastic machinery screw body material manufacturers use 38CrMoAl (Advanced nitriding steel), and some use 42CrMo.
38CrMoAl is a kind of advanced nitriding steel, which is mainly used for nitriding parts with high wear resistance, high fatigue strength and accurate size after heat treatment, or various nitriding parts with low impact load but high wear resistance, such as boring bar, grinder spindle, automatic lathe spindle, worm, precision screw, precision gear, high pressure valve, stem, gauge, template, roller, imitation mold, cylinder block, etcPiston rod of compressor, governor, rotating sleeve and fixed sleeve of steam turbine, various wear-resistant parts of rubber and plastic extruder, etc.
Surfacing technology
1.Surfacing material
Nickel based alloy powder (general nickel 60) and nickel based carbide powder (adding corresponding proportion of carbide powder with nickel 60 as base powder according to product demand).
2.Powder requirements
(1) According to the required properties of the products (wear resistance, corrosion resistance, high temperature resistance), choose the appropriate alloy powder.
(2) The thermal expansion coefficient of alloy powder should be close to that of matrix material.In order to avoid the thermal expansion coefficient is too large, resulting in greater shrinkage stress, resulting in product cracking.The cracking can also be controlled by preheating and heat preservation.
(3) The alloy powder is self melting powder with good fluidity (spherical powder is the best) and uniform particle size.The stability of surfacing can be improved.
(4) The powder feeding speed is uniform, and the speed is generally 10-30g / min.The best particle size range is 150-300 mo.Gas flow range 2.0-2.5l/min
3.Screw requirements
The surfacing surface needs the screw of surfacing alloy powder, and the premise is to ensure that the screw surface is free of oil, rust and obvious defects.
4.Equipment requirements
The equipment is composed of plasma powder welding machine and automatic welding equipment.
(1) Plasma powder stack welding machine
There are three kinds of plasma powder stack welding machines produced by our company: dml-v02bd (100a), dml-v03ad (160A) and dml-v03bd (300A). The power varies from large to small, which can be selected according to the actual working conditions.The main engine power supply adopts highly integrated design, with superior performance and small volume. The refrigeration water tank is equipped with high-power compressor, which can keep the refrigeration water at constant temperature for a long time and ensure the continuous working demand for a long time.
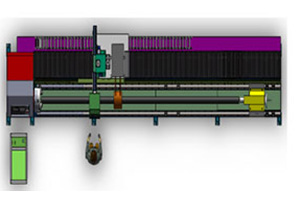
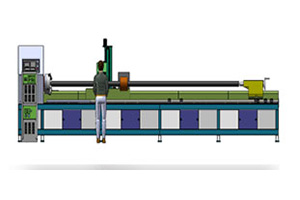
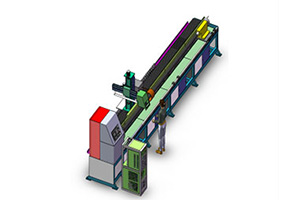