I. Overview of the principles
Plasma cladding is an advanced cladding process that uses hydrogen plasma arc as the heat source and powder alloy as the filler material. Compared with the traditional electric welding, hydrogen arc welding and other cladding methods, plasma powder cladding exists cladding molding, melt depth can be controlled, high bonding, good density, easy to realize the automation and other characteristics, and therefore is also the most suitable for the valve enterprise to apply for special equipment manufacturing license.
Valve companies apply for special equipment manufacturing license (TS) A-level certification, the relevant certification department requires the necessary equipment.
Plasma powder cladding equipment workflow
(1) Arc generation
There are two types of arc generators inside the equipment, supplying non-transfer arc and transfer arc respectively. The negative poles of the two power sources are connected together in parallel and connected to the dove electrode (negative pole) of the welding gun through a cable. The positive terminal of the non-transferred arc power supply is connected to the nozzle of the stacking gun via a cable, and the positive terminal of the transfer arc power supply is connected to the workpiece via a cable. Cooling water is led to the welding gun via water-cooled cables to cool the nozzle and electrode. Hydrogen gas enters the cladding gun through a solenoid valve and float flow meter. When the power supply is turned on, the non-transferring arc is ignited by a high-frequency spark. The non-transfer arc is then ignited by the conductive path created by the flame of the non-transfer arc between the dove electrode and the workpiece. After the ignition of the transfer arc, it can keep or cut off the non-transfer arc.
Retain or cut off the non-transfer arc. The main use of the transfer arc on the surface of the workpiece to produce a molten pool.
(2) welding powder output
Alloy powder is continuously supplied by the powder feeder according to the required amount, and is sent into the welding torch with the help of powder feeding airflow (generally hydrogen) and blown into the arc. Alloy powder in the arc column is pre-heated, molten or semi-molten state, sprayed into the workpiece molten pool, in the molten pool fully melted and discharged.
pool is fully melted, and gas is discharged and slag floats out.
(3) Parameter adjustment
By adjusting the transfer arc and non-transfer arc current, the amount of powder feeding and other parameters of the process specification to control the melting alloy powder and the heat transferred to the workpiece. With the relative movement of the welding torch and the workpiece, the alloy melt pool gradually solidified, on the workpiece to obtain the desired alloy deposition layer.
The desired alloy layer is obtained on the workpiece.
Characteristics of plasma powder cladding process
Plasma cladding due to the use of plasma arc as a heat source and the use of alloy powder as filler metal, which has many advantages compared with other surface cladding methods.
Compared with other surface cladding methods, it has many advantages.
• (1)fast cladding speed, high productivity.
• (2) Controllable melting depth, low dilution rate.
• (3) Surfacing surface is flat and smooth, high density, can realize 0.5-5mm surfacing surface at a time.
• (4) The process stability is good, the spray welding layer quality is high, can be a long time continuously obtain stable surfacing layer, and surfacing surface without porosity,No porosity, trachoma and other surfacing quality problems on the surfacing surface.
• (5) alloy powder preparation is simple, the use of a wide range of materials, you can choose to use drill-based, Jin-based, iron-based, copper-based powder welding consumables, and can be directly formulated according to the working conditions.And it can be directly formulated according to the working conditions.
• (6) It can be equipped with special machines and robots according to requirements, which is easy to realize automation and reduce labor intensity.
II. Equipment composition
The equipment mainly consists of plasma powder welding machine and automatic welding tooling (optional).
1. Plasma Powder Surfacing Welding Machine
Our company produces a total of three kinds of plasma powder cladding machine: DML-V02BD (100A), DML-V03AD (160A), DML-V03BD (300A), the power has a large and small, according to the actual working conditions demand selection. The host power supply adopts highly integrated
The power supply of the host adopts highly integrated design, superior performance and small volume, and the refrigeration tank is installed with high-power compressor, which can keep the chilled water at a constant temperature for a long time, ensuring the continuous work for a long time.
It can keep the chilled water in constant temperature for a long time and ensure the long time continuous working demand.
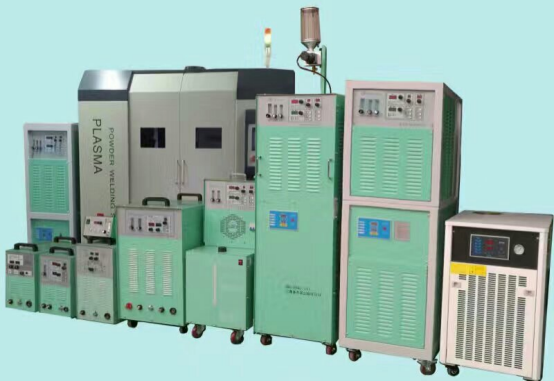
Fig. 1 Integration of multiple plasma powder cladding equipment
2.Automatic Surfacing Machines
For valve sealing surface surfacing, our company developed a variety of special surfacing machine, applicable to eccentric butterfly valves, gate valves, ball valves, globe valves, regulating valves and other general-purpose valves in the field, and has served in Shanghai Valve Factory Co.
Ltd. and dozens of valve manufacturers such as Zhejiang Lianda Valve Group Co.
Specialized machine adopts the way of the overall positioner and mechanical arm, with stepping motor (optional servo motor), linear slide, pendulum, arc pressure tracking device.
The machine is equipped with stepping motor (optional servo motor), linear slide rail, pendulum, arc pressure tracking device (optional), etc., which makes the traveling accurate and the vibration small. Specialized machine control system using PLC system, built-in
A variety of cladding programs, can be programmed for a variety of complex products, easier to operate than ordinary CNC system.
In addition, CNC control system can also be added according to customer requirements. The rotary mechanism is driven by a precision rotary support mechanism, which has a high bearing capacity and high rotary accuracy, and the rotary mechanism is driven by a precision rotary support mechanism.
The rotary mechanism is driven by precision rotary support mechanism with high load bearing and high rotary precision, and is controlled by servo motor, which makes the rotary angle accurate.
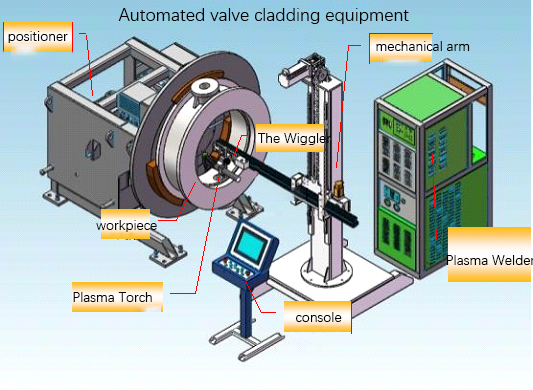
Fig.2 Valve automatic cladding machine reference design diagram
III. Effective photos
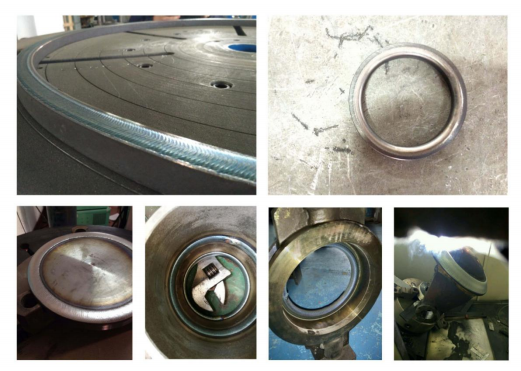
Fig.3 Part of the valve sealing surface cladding photos
Post time: Oct-28-2024