Prinzip und Einführung des Laserauftragschweißens
Beschichtungsverfahren: Das Laserauftragschweißen lässt sich grob in zwei Kategorien einteilen, je nachdem, wie die Beschichtungsmaterialien geliefert werden: voreingestelltes Laserauftragschweißen und synchrones Laserauftragschweißen.
Bei der voreingestellten Laserbeschichtung wird das Beschichtungsmaterial vorab auf dem Verkleidungsteil der Substratoberfläche platziert und dann mit Laserstrahlbestrahlung gescannt und geschmolzen.Das Mantelmaterial wird in Form von Pulver oder Draht hinzugefügt, wobei die Form von Pulver am häufigsten verwendet wird.
Beim synchronen Laserauftragschweißen werden Pulver- oder Drahtbeschichtungsmaterialien während des Beschichtungsprozesses synchron durch die Düse in das Schmelzbad geschickt.Das Mantelmaterial wird in Form von Pulver oder Draht hinzugefügt, wobei die Form von Pulver am häufigsten verwendet wird.
Der Hauptprozess der voreingestellten Laserbeschichtung ist: Vorbehandlung der Substratoberfläche – voreingestelltes Beschichtungsmaterial – Vorwärmen – Laserbeschichtung – Nachwärmebehandlung.
Der Hauptprozessablauf des synchronen Laserauftragschweißens ist: Vorbehandlung der Substratmanteloberfläche --- Vorwärmen --- synchrones Laserauftragschweißen --- Nachwärmebehandlung.
Gemäß dem Prozessablauf handelt es sich bei den Prozessen im Zusammenhang mit der Laserbeschichtung hauptsächlich um die Methode zur Vorbehandlung der Substratoberfläche, die Methode zur Zuführung des Beschichtungsmaterials, das Vorheizen und die Nachwärmebehandlung.
Laser-Funktionsprinzip:
Das komplette Set der Laserauftragschweißausrüstung besteht aus: Laser, Kühleinheit, Pulverzufuhrmechanismus, Bearbeitungstisch usw.
Auswahl der Laser: Gängige Lasertypen unterstützen den Laserauftragsprozess, wie CO2-Laser, Festkörperlaser, Faserlaser, Halbleiterlaser usw.
Prozessparameter
Zu den Prozessparametern der Laserbeschichtung gehören hauptsächlich Laserleistung, Punktdurchmesser, Beschichtungsgeschwindigkeit, Defokusmenge, Pulverzufuhrgeschwindigkeit, Scangeschwindigkeit, Vorwärmtemperatur usw. Diese Parameter haben einen großen Einfluss auf die Verdünnungsrate der Beschichtungsschicht, Risse und Oberflächenrauheit und Kompaktheit der Verkleidungsteile.Die Parameter beeinflussen sich auch gegenseitig, was ein sehr komplizierter Prozess ist, und es müssen angemessene Kontrollmethoden verwendet werden, um diese Parameter innerhalb des zulässigen Bereichs des Laserauftragprozesses zu kontrollieren.
Beim Laserauftragschweißen gibt es drei wichtige Prozessparameter
Laserleistung
Je größer die Laserleistung, desto größer die Menge an geschmolzenem Hüllmetall und desto größer die Wahrscheinlichkeit einer Porosität.Mit zunehmender Laserleistung nimmt die Tiefe der Mantelschicht zu, das umgebende flüssige Metall schwankt heftig und die dynamische Erstarrung kristallisiert, so dass die Anzahl der Poren allmählich abnimmt oder sogar beseitigt wird und auch die Risse allmählich reduziert werden.Wenn die Mantelschichttiefe die Grenztiefe erreicht, steigt mit zunehmender Leistung die Oberflächentemperatur des Substrats und das Verformungs- und Rissphänomen verstärkt sich.Ist die Laserleistung zu gering, schmilzt nur die Oberflächenbeschichtung und das Substrat schmilzt nicht.Zu diesem Zeitpunkt treten lokale Risse auf der Oberfläche der Mantelschicht auf.Pilling, Hohlräume usw. erfüllen nicht den Zweck einer Oberflächenverkleidung.
Spotdurchmesser
Der Laserstrahl ist im Allgemeinen kreisförmig.Die Breite der Mantelschicht hängt hauptsächlich vom Punktdurchmesser des Laserstrahls ab, der Punktdurchmesser nimmt zu und die Mantelschicht wird breiter.Unterschiedliche Punktgrößen führen zu Veränderungen in der Energieverteilung auf der Oberfläche der Mantelschicht, und die resultierende Morphologie und Mikrostruktureigenschaften der Mantelschicht sind sehr unterschiedlich.Im Allgemeinen ist die Qualität der Mantelschicht besser, wenn die Punktgröße klein ist, und die Qualität der Mantelschicht nimmt mit zunehmender Punktgröße ab.Allerdings ist der Spotdurchmesser zu klein, was der Erzielung einer großflächigen Mantelschicht nicht förderlich ist.[3]
Verkleidungsgeschwindigkeit
Die Cladding-Geschwindigkeit V hat einen ähnlichen Effekt wie die Laserleistung P. Ist die Cladding-Geschwindigkeit zu hoch,das Legierungspulverkann nicht vollständig geschmolzen werden und die Wirkung einer hochwertigen Verkleidung wird nicht erreicht;Wenn die Beschichtungsgeschwindigkeit zu niedrig ist, bleibt das Schmelzbad zu lange bestehen, das Pulver verbrennt zu stark, die Legierungselemente gehen verloren und der Wärmeeintrag der Matrix ist groß.wird das Ausmaß der Verformung erhöhen.
Die Parameter der Laserbeschichtung beeinflussen die makroskopische und mikroskopische Qualität der Beschichtungsschicht nicht unabhängig voneinander, sondern beeinflussen sich gegenseitig.Um den umfassenden Effekt von Laserleistung P, Spotdurchmesser D und Mantelgeschwindigkeit V zu veranschaulichen, wird das Konzept der spezifischen Energie Es vorgeschlagen, nämlich:
Es=P/(DV)
Das heißt, die Bestrahlungsenergie pro Flächeneinheit und Faktoren wie LaserLeistungsdichteund Mantelgeschwindigkeit können zusammen betrachtet werden.
Die Reduzierung der spezifischen Energie ist vorteilhaft für die Reduzierung der Verdünnungsrate und steht auch in gewissem Zusammenhang mit der Dicke der Mantelschicht.Unter der Bedingung einer konstanten Laserleistung nimmt die Verdünnungsrate der Mantelschicht mit zunehmendem Punktdurchmesser ab, und wenn die Mantelgeschwindigkeit und der Punktdurchmesser konstant sind, steigt die Verdünnungsrate der Mantelschicht mit zunehmender Laserstrahlleistung.Darüber hinaus nimmt mit zunehmender Mantelgeschwindigkeit die Schmelztiefe des Substrats ab und die Verdünnungsrate der Mantelschicht vom Substratmaterial nimmt ab.
Beim Multi-Pass-Laserauftragschweißen ist die Überlappungsrate der Haupteinflussfaktordie Oberflächenrauheitder Mantelschicht.Wenn die Überlappungsrate zunimmt, nimmt die Oberflächenrauheit der Mantelschicht ab, aber die Gleichmäßigkeit des überlappten Teils kann nur schwer garantiert werden.Die Tiefe des Überlappungsbereichs zwischen den Verkleidungsbahnen unterscheidet sich von der Tiefe der Mitte der Verkleidungsbahnen, was sich auf die Gleichmäßigkeit der gesamten Verkleidungsschicht auswirkt.Darüber hinaus wird die Zugeigenspannung einer mehrlagigen Umhüllung überlagert, was den lokalen Gesamtspannungswert erhöht und die Rissempfindlichkeit der Umhüllungsschicht erhöht.Durch Vorwärmen und Anlassen kann die Rissneigung der Mantelschicht verringert werden.
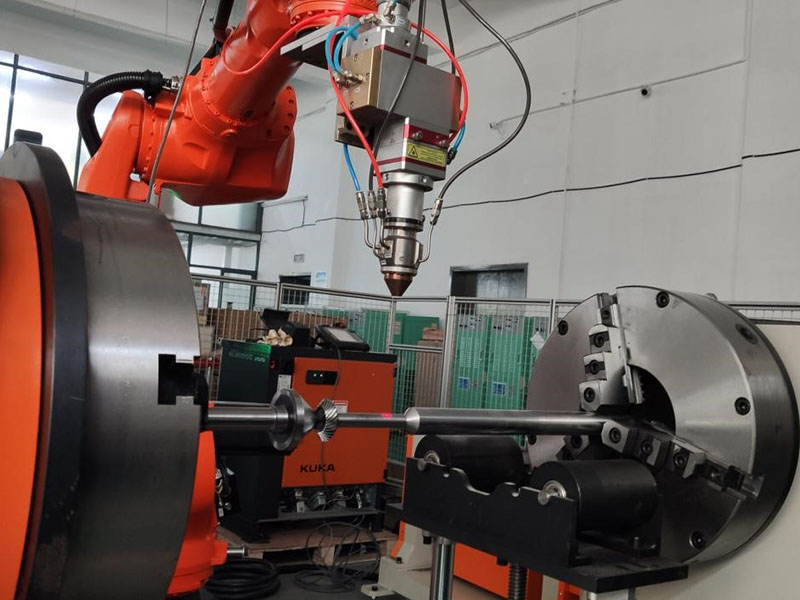
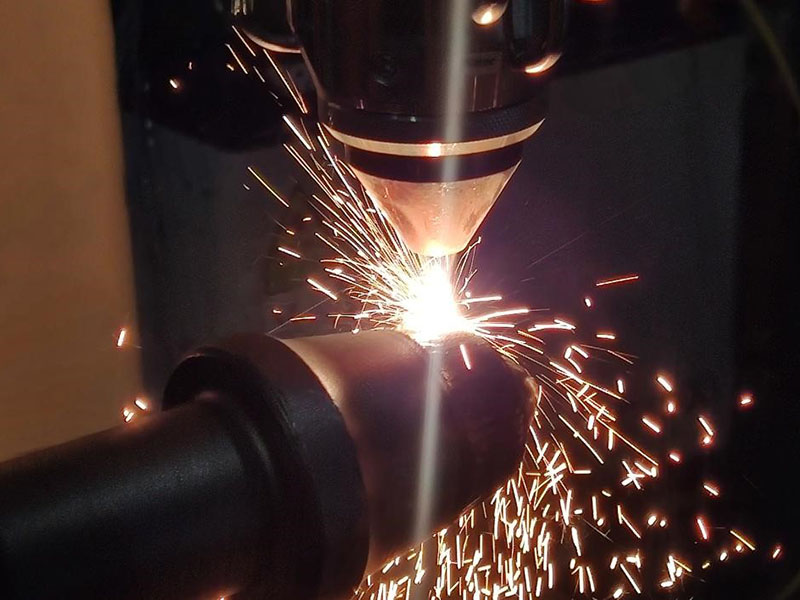
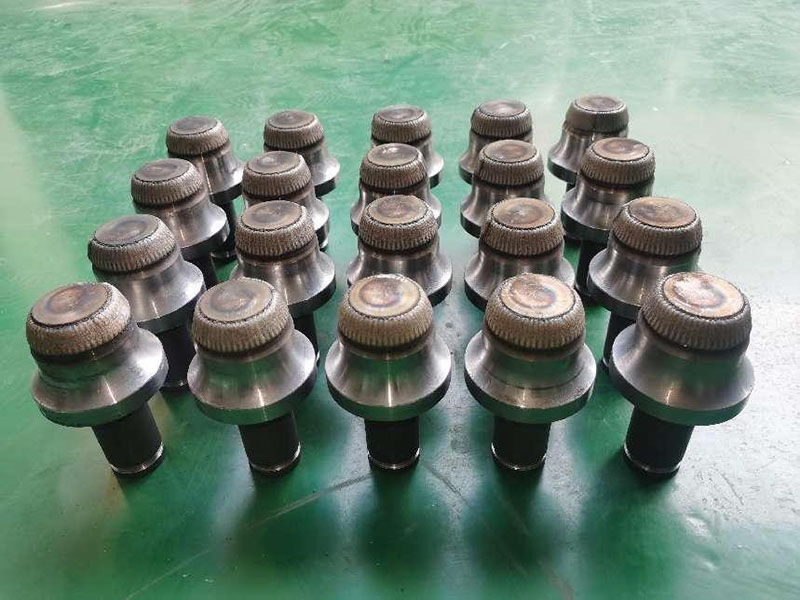
Zeitpunkt der Veröffentlichung: 15. August 2023