Principles of the EDM deposition process
EDM deposition process is the power supply stored high energy energy between the metal electrode and the base material instantaneous high-frequency release, through the electrode material and the base material between the gas ionization, the formation of a number of micro-arc channels, so that the surface of the base material to produce instantaneous high-temperature micro-area, electrode material in the micro-electric field under the action of the fusion welded to the base material substrate, the formation of the metallurgical bond. EDM process is a micro-area of repeated instantaneous high temperature - cooling process, it is different from traditional welding, solid basically no high temperature rise, and therefore will not produce stress, deformation and other phenomena.
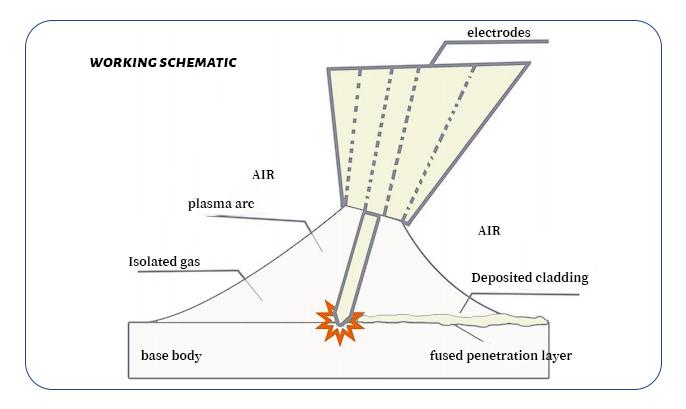
Technical features
The EDM deposition process, also known as arc cladding, is a process that utilizes the heat generated by an electric spark discharge to melt and deposit metallic materials. Its main advantages and benefits are:
1. High precision: Since EDM is realized by precisely controlling the current and voltage, the cladding process is very precise and can achieve accurate shape and size control.
2. High efficiency: EDM cladding is relatively fast and can quickly repair or enhance localized worn or damaged parts of the workpiece, increasing productivity.
3. Flexibility: This process is suitable for a variety of complex shapes and small areas of repair, regardless of the shape and size of the workpiece.
4. Small heat-affected zone: Compared with conventional welding, the heat-affected zone of EDM cladding is small, which has less influence on the deformation and stress of the workpiece and retains the original performance of the workpiece.
5. Wide choice of materials: Almost all metal materials can be repaired or enhanced by EDM cladding, including cemented carbide, stainless steel, aluminum alloys and so on.
6. Environmentally friendly: Compared with fusion welding, EDM cladding emits less fumes and harmful gases and has less impact on the environment.
7. On-line repair: Without stopping production, repair can be carried out on running equipment, which is very favorable for the maintenance of some critical equipment.
Overall, the EDM deposition process is a fast, precise, flexible and environmentally friendly means of repair and strengthening.
Repair of cast iron shell surface defects
EDM Surfacing Deposition Process VS Conventional Patch Welding
EDM deposition process (Plasma Arc Welding) and traditional filler welding (MIG Welding) are commonly used welding technology, but they have certain differences in principle, advantages and disadvantages and scope of application.
1. The principle is different: EDM deposition process uses electric spark as the welding heat source, through the high-frequency electromagnetic field to produce high-temperature, low-pressure electric spark, so as to realize the material fusion. Traditional filler welding adopts lithium oxide current welder (MIG gun) as the heat source, and realizes welding by shielding the welding area with gases such as lithium oxide alkane (CO2) or nitrogen oxide alkane (Argon).
2. Differences in precision: The EDM buildup deposition process offers high precision and weld capsule density, making it suitable for weldments that require high precision and strength. Conventional filler welding, although it performs well in many applications, has a slightly lower precision and weld capsule density than the EDM deposition process.
3. Different scope of application: EDM deposition process is applicable to a variety of metal materials, including steel, aluminum, nickel, lead, etc., and has a wide range of applications. The traditional repair welding is mainly applied to fiber rubber, alloy, aluminum and other materials, its scope of application is relatively narrow.
4. Different environmental performance: EDM deposition process does not produce hazardous waste and has better environmental performance. In traditional filler welding, if lithium oxide (CO2) is used as a shielding gas, it may produce hazardous waste and affect the environment.
5. Differences in operating difficulty: The EDM deposition process is relatively simple to operate and has a high degree of maneuverability. While the traditional filler welding is more complicated in terms of operation difficulty and requires more skills and experience.
In short, there are some differences between EDM deposition process and traditional filler welding in terms of principle, precision, scope of application, environmental performance and operational difficulty. According to the specific application needs and material type, you can choose the most suitable welding technology.
Related Product Links
https://www.ourcladding.com/intelligent-edm-cladding-repair-machine-esd-9100-product/
https://www.youtube.com/watch?v=8vFi1XloPQI
Post time: Apr-08-2024