1.1 The effect of current on the molding of the cladding layer
Current(A) |
Depth (of fusion)(mm) |
Floor height(mm) |
width(mm) |
70 |
0.19 |
4.26 |
16.41 |
80 |
0.35 |
4.07 |
17.08 |
90 |
0.88 |
3.43 |
17.48 |
100 |
1.03 |
2.73 |
17.58 |
110 |
1.25 |
2.65 |
18.14 |
Table 3.1 Geometry of cross-section of cladding layer with different currents
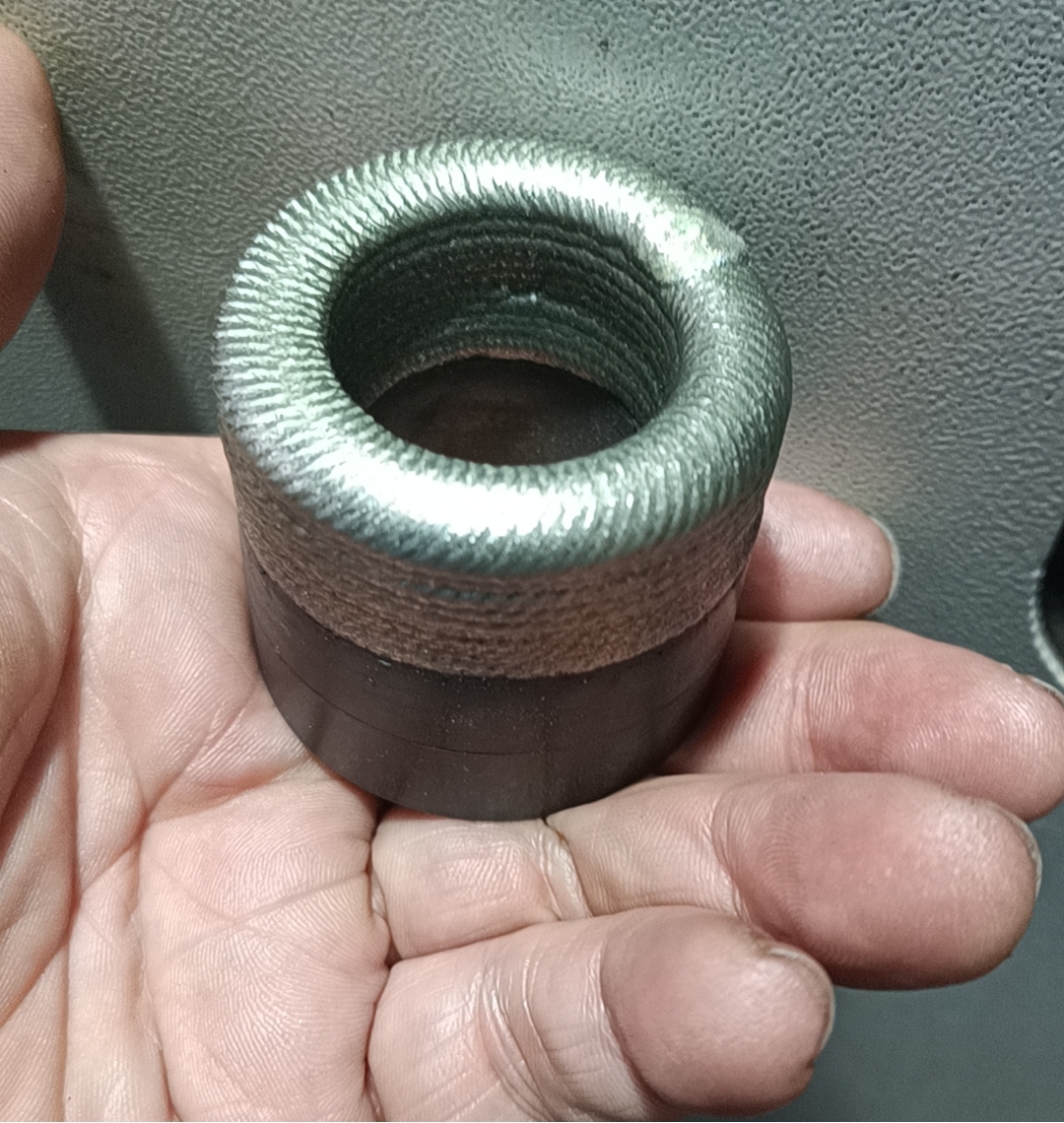
As the current increases, the depth and width of the cladding layer increases and the layer height decreases. This is due to the increase in current, the heat generated will not only melt the cladding metal, but also part of the substrate melting, cladding and substrate mixing occurs, so that the cladding layer as a whole subsidence, resulting in an increase in the depth of fusion, the layer height decreases; and increase the current, making the plasma arc is more coarse, increase the temperature range of the heat source, the molten pool in the substrate spread ability is stronger, so the width of the molten pool increases.
1.2 The effect of welding speed on the molding of the molten cladding layer
Welding speed(mm/s) |
Depth (of fusion)(mm) |
Floor height(mm) |
width(mm) |
4 |
1.17 |
4.34 |
17.61 |
5 |
1.06 |
2.73 |
17.58 |
6 |
0.35 |
2.61 |
16.96 |
7 |
0.13 |
2.55 |
15.01 |
8 |
— |
— |
— |
Table 3.2 Cross-sectional geometry of molten cladding layers with different welding speeds
With the increase of welding speed, the depth of fusion of the cladding layer decreases, the layer height shows first a sharp decrease and then slowly become smaller, the width decreases. When the welding speed is 4 mm/s, with the increase of the cladding metal to a certain extent, the depth of fusion is 1.17 mm, at this time, the heat input per unit length can not make the base material to further melt, the fusion cladding layer continues to pile up the height of the layer height of 4.34 mm; the welding speed increases to 5 mm/s, the heat input per unit length, the amount of wire feeding are reduced, so the depth of fusion, layer height, width are reduced; if the welding speed continues to increase, as mentioned above, the heat input is insufficient at this time, only a small part of the base material can melt, the fusion cladding layer height shows a sharp decrease first and then slowly become smaller, width is reduced. If the welding speed continues to increase, as mentioned above, the heat input at this time is insufficient, only a small part of the base material can be melted, the fusion cladding layer does not appear to be sagging, resulting in a greater reduction in the depth of fusion, while the layer height is reduced less.
1.3 Influence of wire feeding speed on the molding of the cladding layer
Wire-feeding spped(mm/s) |
Depth (of fusion)(mm) |
Floor height(mm) |
width(mm) |
40 |
1.43 |
2.24 |
19.91 |
50 |
1.25 |
2.56 |
18.86 |
60 |
1.03 |
2.73 |
17.58 |
70 |
0.71 |
3.46 |
15.82 |
80 |
0.16 |
5.16 |
14.20 |
Table 3.3 Geometric dimensions of the cross-section of the cladding layer with different wire feeding speeds.
As the wire feed speed increases, the depth and width of the cladding layer decreases and the layer height increases. This is due to the fact that when the current and welding speed are certain, the heat input per unit length is certain, and with the increase of wire feeding speed, the amount of filler wire per unit length is increased, and the cladding metal needs to absorb more heat, and when the heat input is unable to completely melt the whole cladding layer, the base material part is less melted, so the depth of melting decreases, and the height of the layer increases, and the spreading capacity of the cladding metal close to the base material part deteriorates, so the width decreases rapidly. The width will decrease rapidly.
In summary, the plasma arc cladding 2205 duplex stainless steel layer effective process parameters range from: current 90 A ~ 110 A, welding speed 4 mm / s ~ 6 mm / s, wire feeding speed 50 mm / s ~ 70 mm / s, the ion gas flow rate of 1.5 L / min.
2 Based on the response surface method of fusion cladding layer forming process parameters optimization
Response surface method (Response surface method, RSM) is a combination of experimental design and statistical techniques of optimization methods, the analysis of test data, can be derived from the impact factor and the response value of the fitting function and three-dimensional surface map, can intuitively reflect the impact factor and the response value of the relationship between the actual test has a predictive, optimization role. Based on the above reasons, the selection of RSM in the central composite design (Central composite design, CCD) to develop process optimization program, to explore the current, welding speed, wire feeding speed and the fusion cladding layer dilution rate, aspect ratio of the relationship between the current, welding speed, wire feeding speed and the fusion cladding layer dilution rate, and mathematical modeling, derived from the process parameters and the dilution rate, aspect ratio of the function, to achieve the prediction of fusion cladding layer quality.
2.1 The influence of process parameters on the dilution rate of the cladding layer.
Table 3.8 Process optimization results and verification
Group |
X1(A) |
X2(mm·s-1) |
X3(mm·s-1) |
dilution ratio(%) |
aspect ratio |
Prediction Group |
99 |
6 |
50 |
14.8 |
4.36 |
Test Group 1 |
99 |
6 |
50 |
13.9 |
4.13 |
Test Group 2 |
99 |
6 |
50 |
15.5 |
4.56 |
Test Group 3 |
99 |
6 |
50 |
14.3 |
4.27 |
Average error |
2.9 |
2.3 |
(PTA welding by Shanghai Duomu)
Figure 3.16 Optimal process parameters test results (a) Test group 1; (b) Test group 2; (c) Test group 3
High-quality cladding layer seeks to have a small dilution rate and a large aspect ratio. The optimal process parameters are: current 99 A, welding speed 6 mm-s-1, wire feeding speed 50 mm-s-1. The average dilution rate of the cladding layer prepared under the optimal process is about 14.6%, and the average aspect ratio is 4.33, and the average error between the model prediction value and the experimental value is less than 5%, which indicates that the model has a high degree of accuracy, and the quality of the cladding layer formed under the optimal process is good.
Post time: Jan-31-2024