1.1 Wpływ prądu na formowaniewarstwa okładzinowa
Aktualny(A) | Depth (fuzji)(mm) | Fwysokość podłogi(mm) | szerokość(mm) |
70 | 0,19 | 4.26 | 16.41 |
80 | 0,35 | 4.07 | 17.08 |
90 | 0,88 | 3,43 | 17.48 |
100 | 1.03 | 2,73 | 17.58 |
110 | 1,25 | 2,65 | 18.14 |
Tabela 3.1 Geometria przekroju warstwy okładzinowej przy różnych prądach
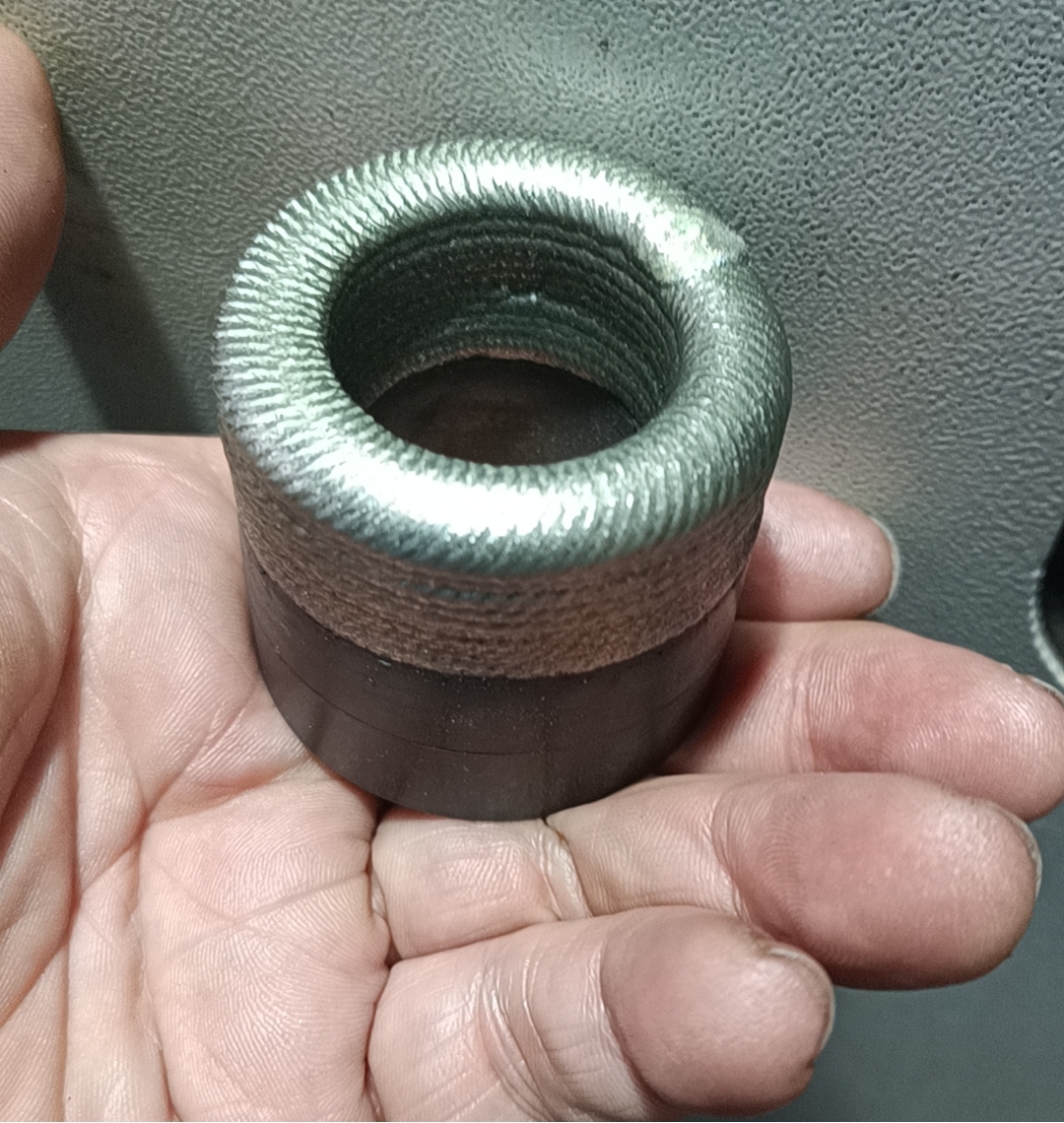
Wraz ze wzrostem prądu zwiększa się głębokość i szerokość warstwy okładziny, a wysokość warstwy maleje.Dzieje się tak na skutek wzrostu prądu, wytworzone ciepło nie tylko stopi metal okładziny, ale także nastąpi stopienie części podłoża, okładziny i wymieszanie podłoża, w wyniku czego warstwa okładziny jako całość osiada, co skutkuje wzrostem głębokość wtopienia, wysokość warstwy maleje;i zwiększ prąd, powodując, że łuk plazmowy jest bardziej gruby, zwiększ zakres temperatur źródła ciepła, zdolność roztopionego jeziorka w podłożu jest silniejsza, więc szerokość stopionego jeziorka wzrasta.
1.2 Efektspawalniczyprędkość formowania stopionej warstwy okładzinowej
Prędkość spawania(mm/s) | Depth (fuzji)(mm) | Fwysokość podłogi(mm) | szerokość(mm) |
4 | 1.17 | 4,34 | 17.61 |
5 | 1.06 | 2,73 | 17.58 |
6 | 0,35 | 2.61 | 16,96 |
7 | 0,13 | 2,55 | 15.01 |
8 | — | — | — |
Tabela 3.2 Geometria przekroju poprzecznego warstw stopionego napawania przy różnych prędkościach spawania
Wraz ze wzrostem prędkości zgrzewania zmniejsza się głębokość wtopienia warstwy napawania, wysokość warstwy najpierw gwałtownie maleje, a następnie powoli maleje, a szerokość maleje.Gdy prędkość spawania wynosi 4 mm/s, przy pewnym wzroście metalu okładziny głębokość wtopienia wynosi 1,17 mm, w tym momencie doprowadzone ciepło na jednostkę długości nie może spowodować dalszego stopienia materiału podstawowego, warstwa okładziny termotopliwej nadal spiętrza się do wysokości warstwy wynoszącej 4,34 mm;prędkość spawania wzrasta do 5 mm/s, zmniejsza się dopływ ciepła na jednostkę długości, zmniejsza się ilość podawanego drutu, a co za tym idzie, zmniejsza się głębokość wtopu, wysokość warstwy, szerokość;jeśli prędkość spawania będzie nadal rosła, jak wspomniano powyżej, dopływ ciepła jest w tym momencie niewystarczający, tylko niewielka część materiału podstawowego może się stopić, wysokość warstwy napawania najpierw gwałtownie spada, a następnie powoli maleje, szerokość jest zredukowany.Jeśli prędkość spawania będzie nadal rosła, jak wspomniano powyżej, doprowadzone ciepło w tym momencie będzie niewystarczające, tylko niewielka część materiału podstawowego może się stopić, a warstwa napawania nie wydaje się zwisać, co skutkuje większym zmniejszeniem głębokość wtopienia, podczas gdy wysokość warstwy zmniejsza się w mniejszym stopniu.
1.3 Wpływ prędkości podawania drutu na kształtowanie warstwy napawacza
Prędkość podawania drutu(mm/s) | Depth (fuzji)(mm) | Fwysokość podłogi(mm) | szerokość(mm) |
40 | 1,43 | 2.24 | 19.91 |
50 | 1,25 | 2,56 | 18.86 |
60 | 1.03 | 2,73 | 17.58 |
70 | 0,71 | 3,46 | 15.82 |
80 | 0,16 | 5.16 | 14.20 |
Tabela 3.3 Wymiary geometryczne przekroju warstwy napawania przy różnych prędkościach podawania drutu.
Wraz ze wzrostem prędkości podawania drutu głębokość i szerokość warstwy napawania maleje, a wysokość warstwy wzrasta.Dzieje się tak dlatego, że gdy prąd i prędkość spawania są pewne, to ilość dostarczonego ciepła na jednostkę długości jest pewna, a wraz ze wzrostem prędkości podawania drutu zwiększa się ilość drutu dodatkowego na jednostkę długości, a zapotrzebowanie na metal okładzinowy pochłaniać więcej ciepła, a gdy doprowadzone ciepło nie jest w stanie całkowicie stopić całej warstwy okładziny, część materiału bazowego jest mniej stopiona, więc głębokość topienia maleje, a wysokość warstwy wzrasta, a zdolność rozprzestrzeniania się okładziny metal w pobliżu części z materiału podstawowego ulega zniszczeniu, więc szerokość szybko się zmniejsza.Szerokość będzie się szybko zmniejszać.
Podsumowując, efektywne parametry procesu napawania łukiem plazmowym 2205 ze stali nierdzewnej duplex mieszczą się w zakresie: prąd 90 A ~ 110 A, prędkość spawania 4 mm/s ~ 6 mm/s, prędkość podawania drutu 50 mm/s ~ 70 mm/s, natężenie przepływu gazu jonowego 1,5 l/min.
2 Oparta na metodzie powierzchni odpowiedzi optymalizacji parametrów procesu kształtowania warstwy okładziny stapianej
Metoda powierzchni odpowiedzi (metoda powierzchni odpowiedzi, RSM) to połączenie projektowania eksperymentalnego i technik statystycznych metod optymalizacji, analiza danych testowych, można wyprowadzić ze współczynnika wpływu i wartości odpowiedzi funkcji dopasowania i trójwymiarowej mapy powierzchni , może intuicyjnie odzwierciedlać współczynnik wpływu, a wartość odpowiedzi związku pomiędzy rzeczywistym testem ma rolę predykcyjną, optymalizacyjną.W oparciu o powyższe powody wybór RSM do centralnego projektu kompozytu (Central Composite Design, CCD) w celu opracowania programu optymalizacji procesu, zbadania prądu, prędkości spawania, prędkości podawania drutu i stopnia rozcieńczenia warstwy napawania stapialnego, współczynnika kształtu związek między prądem, prędkością spawania, prędkością podawania drutu i stopniem rozcieńczenia warstwy napawania, a także modelowanie matematyczne, wyprowadzone z parametrów procesu i stopnia rozcieńczenia, współczynnika kształtu funkcji, w celu uzyskania przewidywania jakości warstwy napawania.
2.1 Wpływ parametrów procesu na stopień rozcieńczenia warstwy okładzinowej.
Tabela 3.8 Wyniki i weryfikacja optymalizacji procesu
Grupa | X1(A) | X2(mm·s-1) | X3(mm·s-1) | współczynnik rozcieńczenia(%) | współczynnik proporcji |
Grupa prognoz | 99 | 6 | 50 | 14.8 | 4,36 |
Grupa testowa 1 | 99 | 6 | 50 | 13.9 | 4.13 |
Grupa testowa 2 | 99 | 6 | 50 | 15,5 | 4,56 |
Grupa testowa 3 | 99 | 6 | 50 | 14.3 | 4,27 |
Przeciętny błąd | 2.9 | 2.3 |
(spawanie PTA przez Shanghai Duomu)
Rysunek 3.16 Wyniki badań optymalnych parametrów procesu (a) Grupa badana 1;b) grupa badana 2;(c) Grupa testowa 3
Wysokiej jakości warstwa okładzinowa wymaga małego stopnia rozcieńczenia i dużego współczynnika kształtu.Optymalne parametry procesu to: prąd 99 A, prędkość spawania 6 mm-s-1, prędkość podawania drutu 50 mm-s-1.Średni stopień rozcieńczenia warstwy okładzinowej przygotowanej w procesie optymalnym wynosi około 14,6%, średni współczynnik kształtu wynosi 4,33, a średni błąd pomiędzy wartością przewidywaną modelu a wartością eksperymentalną jest mniejszy niż 5%, co wskazuje, że model charakteryzuje się dużą dokładnością, a jakość warstwy okładzinowej powstałej w optymalnym procesie jest dobra.
Czas publikacji: 31 stycznia 2024 r