1.1 電流が成形品に及ぼす影響クラッド層
現在(A) | Depth (融合の)(mm) | F床の高さ(mm) | 幅(mm) |
70 | 0.19 | 4.26 | 16.41 |
80 | 0.35 | 4.07 | 17.08 |
90 | 0.88 | 3.43 | 17.48 |
100 | 1.03 | 2.73 | 17.58 |
110 | 1.25 | 2.65 | 18.14 |
表 3.1 電流の異なるクラッド層の断面形状
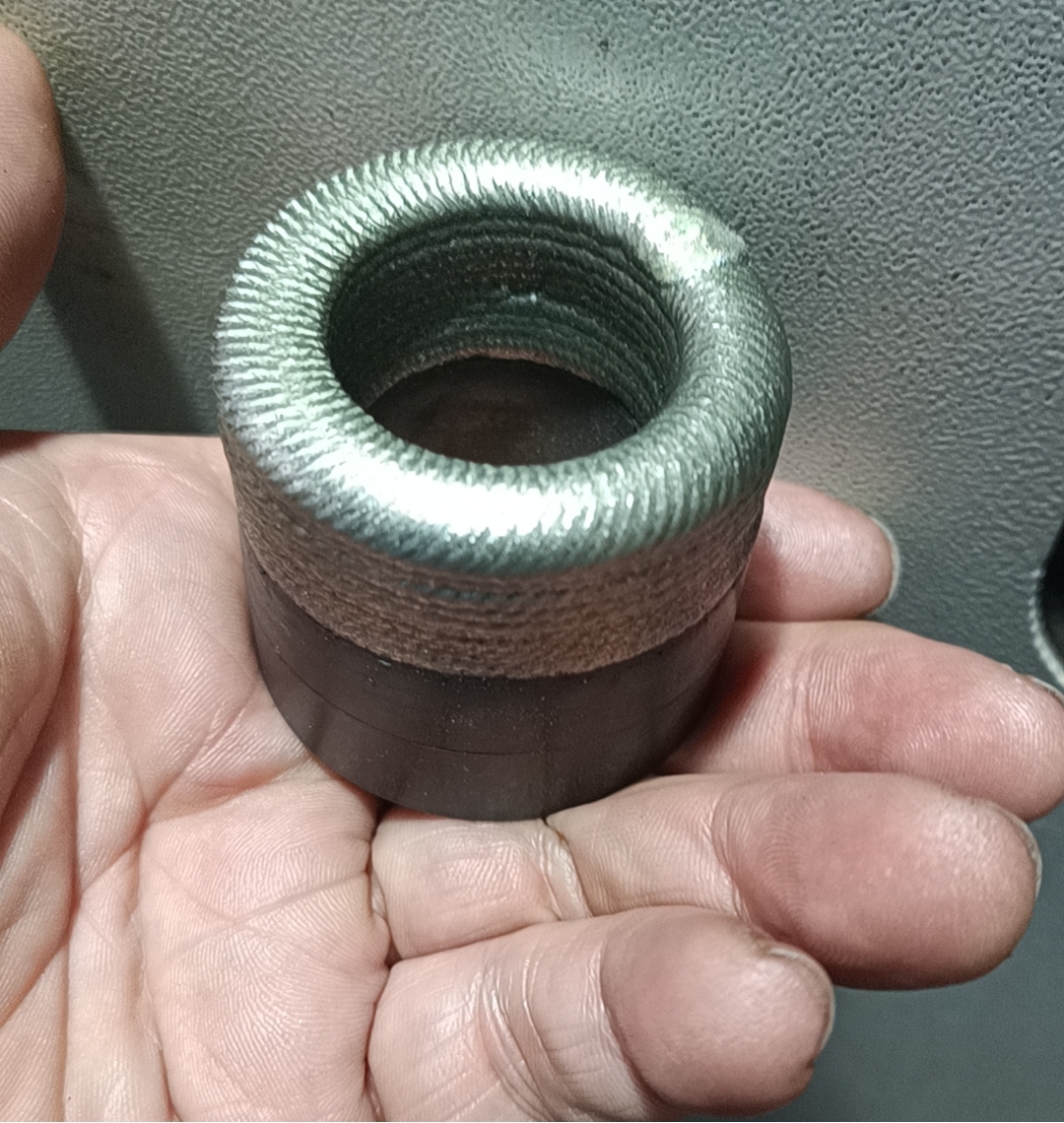
電流が増加すると、クラッド層の深さと幅が増加し、層の高さは減少します。これは、電流の増加により、発生した熱によりクラッド金属が溶融するだけでなく、基材の一部が溶融し、クラッドと基材の混合が起こり、クラッド層全体が沈下し、その結果、融合の深さ、層の高さは減少します。電流を増やすと、プラズマアークがより粗くなり、熱源の温度範囲が増加し、基板内の溶融池の拡散能力が強くなり、溶融池の幅が増加します。
1.2 の影響溶接溶融クラッド層の成形速度
溶接速度(mm/s) | Depth (融合の)(mm) | F床の高さ(mm) | 幅(mm) |
4 | 1.17 | 4.34 | 17.61 |
5 | 1.06 | 2.73 | 17.58 |
6 | 0.35 | 2.61 | 16.96 |
7 | 0.13 | 2.55 | 15.01 |
8 | — | — | — |
表3.2 溶接速度の異なる溶融肉盛層の断面形状
溶接速度の増加に伴い、クラッド層の溶融深さは減少し、層の高さは最初に急激に減少し、その後徐々に小さくなり、幅が減少します。溶接速度が4mm/sの場合、肉盛金属がある程度増加すると、溶融深さは1.17mmとなり、このとき単位長さ当たりの入熱量では母材をそれ以上溶融させることができず、融着被覆層は、層の高さ4.34mmの高さに積み重なり続ける。溶接速度が 5 mm/s に増加し、単位長さあたりの入熱量が減少し、ワイヤ送給量が減少するため、溶融深さ、層の高さ、幅が減少します。溶接速度が増加し続けると、前述したように、この時点での入熱が不十分であり、母材のごく一部のみが溶けることができ、溶融クラッド層の高さは最初に急激な減少を示し、その後ゆっくりと小さくなり、幅は削減。溶接速度が増加し続けると、前述したように、このときの入熱量が不足し、母材の一部しか溶けることができず、溶融肉盛層のたわみが現れず、結果として溶接速度の低下が大きくなります。溶融の深さは減少しますが、層の高さの減少は少なくなります。
1.3 ワイヤ送給速度がクラッド層の成形に及ぼす影響
ワイヤ送給速度(mm/s) | Depth (融合の)(mm) | F床の高さ(mm) | 幅(mm) |
40 | 1.43 | 2.24 | 19.91 |
50 | 1.25 | 2.56 | 18.86 |
60 | 1.03 | 2.73 | 17.58 |
70 | 0.71 | 3.46 | 15.82 |
80 | 0.16 | 5.16 | 14.20 |
表 3.3 ワイヤ送給速度の異なるクラッド層断面の幾何学的寸法。
ワイヤの送り速度が増加すると、クラッド層の深さと幅は減少し、層の高さは増加します。これは、電流と溶接速度が一定であれば単位長さ当たりの入熱量も一定となり、ワイヤ送給速度の増加に伴い単位長さ当たりのフィラーワイヤの量が増加し、被覆金属の必要量が増加するためである。より多くの熱を吸収するため、入熱によってクラッド層全体を完全に溶融できない場合、母材部分の溶融が少なくなり、溶融の深さが減少し、層の高さが増加し、クラッドの広がり能力が低下します。母材部分に近い金属が劣化するため、幅が急激に減少します。幅は急激に減少します。
要約すると、プラズマ アーク クラッド 2205 二相ステンレス鋼層の有効プロセス パラメーターの範囲は次のとおりです。電流 90 A ~ 110 A、溶接速度 4 mm/s ~ 6 mm/s、ワイヤ送給速度 50 mm/s ~ 70 mm/s、イオンガス流量1.5L/min。
2 応答曲面法に基づく融着被覆層形成プロセスパラメータの最適化
応答曲面法(応答曲面法、RSM)は、実験計画法と最適化手法の統計的手法を組み合わせたもので、試験データの分析により、フィッティング関数と 3 次元曲面マップの衝撃係数と応答値から導き出すことができます。 、実際のテスト間の関係のインパクトファクターと応答値を直感的に反映でき、予測、最適化の役割を果たします。上記の理由に基づいて、プロセス最適化プログラムを開発するための中央複合設計(中央複合設計、CCD)での RSM の選択は、電流、溶接速度、ワイヤ送給速度、および溶融被覆層の希釈率、アスペクト比を調査します。電流、溶接速度、ワイヤ送給速度と溶融被覆層の希釈率との関係、およびプロセスパラメータと希釈率、関数のアスペクト比から導出された数学的モデリングにより、溶融被覆層の品質の予測を実現します。
2.1 クラッド層の希釈率に対するプロセスパラメータの影響。
表3.8 プロセス最適化の結果と検証
グループ | X1(A) | X2(mm・s-1) | X3(mm・s-1) | 希釈率(%) | アスペクト比 |
予測グループ | 99 | 6 | 50 | 14.8 | 4.36 |
テストグループ 1 | 99 | 6 | 50 | 13.9 | 4.13 |
テストグループ 2 | 99 | 6 | 50 | 15.5 | 4.56 |
テストグループ 3 | 99 | 6 | 50 | 14.3 | 4.27 |
平均誤差 | 2.9 | 2.3 |
(上海多夢社によるPTA溶接)
図 3.16 最適プロセスパラメータのテスト結果 (a) テストグループ 1。(b) 試験グループ 2;(c) 試験グループ 3
高品質なクラッド層は、希釈率が小さく、アスペクト比が大きいことが求められます。最適なプロセスパラメータは、電流 99 A、溶接速度 6 mm-s-1、ワイヤ送給速度 50 mm-s-1 です。最適なプロセスで調製されたクラッド層の平均希釈率は約 14.6%、平均アスペクト比は 4.33、モデルの予測値と実験値の平均誤差は 5% 未満であり、モデルが適切であることを示しています。精度が高く、最適なプロセスで形成されたクラッド層の品質も良好です。
投稿時刻: 2024 年 1 月 31 日