高速レーザークラッド粉末の利用率に関係する要因は何ですか?
高速レーザークラッディング技術は大幅に向上しました。加工効率の向上と加工コストの削減への追求は終わりがありません。加工コストをいかに削減し続けるかは、依然として高速レーザークラッド研究の重要な内容です。

粉末コストはレーザクラッドの総コストの80%~90%を占めるため、高速レーザクラッドにおいては粉末の利用率の向上が重要な技術課題となっている。したがって、高速レーザークラッドの粉末利用率にどのような要因が関係しているかを調べる必要があります。これらの要因を1つずつ検討し、高速レーザークラッドの粉末利用率を向上させる方法について説明します。
(1) 溶融池のスポットサイズ
高速レーザークラッド粉末の利用率に影響を与える主な要因は、溶融池のスポットサイズ、つまり基板表面に落下するレーザーのスポットサイズです。レーザーパワーに応じて、高速レーザークラッドプールのスポットは1mmから5mmの間で選択できます。実際の作業では、装置のレーザー出力に応じて適切なサイズの溶接池スポットを選択する必要があります。
溶融池のスポットが小さすぎて、粉末の利用率が低い。溶融池のスポットが大きすぎて、めっき表面の平坦性が低下します。溶融池のスポットを大きくすると粉末の利用率は向上しますが、溶融池のスポットが大きすぎると皮膜の平坦性が低下するため、その後の研削・研磨工程でも粉末の無駄が発生します。高速レーザクラッドにおいても、粉末の利用率はクラッド工程のみで考えるのではなく、クラッド工程全体における研削・研磨後の粉末の総合利用率を考慮する必要があります。
(2) クラッドヘッドの粉末出口穴の直径
クラッディング ヘッドの粉末出口穴の直径によって、粉末の流れの厚さが決まります。口径が小さいほど粉体流は細かくなりますが、粉体流が細かいほど粉体流の分散は速くなります。実際の作業では、基板表面の粉末スポット直径がスポットよりも小さくなるように、クラッドの高さと溶融池のスポットサイズに応じて適切な粉末出口穴の直径を選択する必要があります。そうしないと、溶融池のスポット サイズを超える粉末が失われ、無駄になってしまいます。
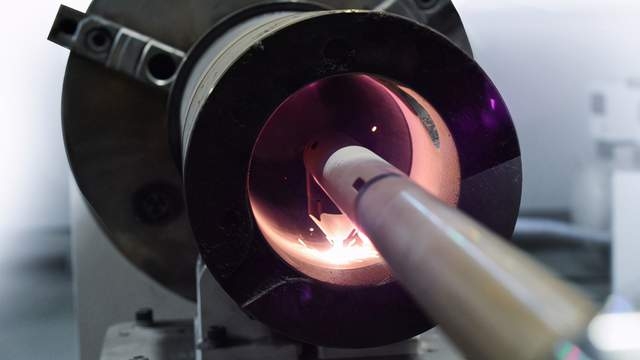
(3) レーザー出力
レーザー出力は、溶融池のスポットに落ちた粉末を完全に溶かすことができるのに十分な大きさである必要があります。粉体の供給量などが一定の場合、レーザーパワーが大きいほど粉体の利用率は高くなります。
(4) 粉体供給サイズ
装置のレーザーパワーが決まると、粉体供給量が少ないほど粉体利用率が高くなります。ただし、粉末供給量を減らすと被覆効率に影響します。クラッド効率を考慮しない場合、粉末供給量を制御することで粉末利用率を100%に到達させることも可能ですが、これでは意味がありません。
(5) 被覆線速度
高速レーザークラッドの線速度は、通常のレーザークラッドの数倍から数十倍にもなります。基板とクラッドヘッドとの相対移動速度が大きい場合、基板表面での粉末粒子の運動エネルギーが大きいため、粉末の排出量が大きくなり、粉末利用率が低下します。また、レーザーパワーを決定する際、クラッドヘッドと基板間の相対移動速度が速いほど、溶融池の温度は低下し、粉末利用率は低下します。
(6) ワーク体積
同じクラッドパラメータでは、ワークピースの直径(体積)が大きくなるほど、粉末利用率は低くなります。これは、体積が大きいとレーザーエネルギーがマトリックスに吸収されやすくなり、溶融池の温度が十分に高くならないためです。したがって、大容量のワークピースの場合は、粉末利用率を向上させるために、より高出力のクラッド装置を使用する必要があります。
(7) 粉末粒子径
高速レーザークラッド粉末は光との相互作用時間が短いため、レーザーパワーの大きさに応じて適切な粒径の粉末を選択する必要があります。粉末粒子が大きいと、限られた時間内に粉末が溶けず、噴射飛沫ロスが発生します。
上記は、高速レーザークラッド粉末の利用率に影響を与える主な 7 つの要因です。粉末の利用率を向上させ、肉盛加工の処理コストを削減するには、装置と肉盛ワークの特定の条件に応じて、適切なハードウェア技術パラメータと肉盛加工パラメータを選択する必要があります。
ここでも、粉末利用率は、単純なクラッドプロセスの粉末利用率ではなく、処理プロセス全体の粉末利用率を考慮する必要があることが強調されます。通常のレーザークラッドの粉末利用率は 100% に達することもありますが、総合的な粉末利用率は 50% 未満であることがよくあります。
投稿日時: 2022 年 8 月 24 日