Weld overlay, also known as cladding, is a technique of depositing metal material on the surface of a workpiece by welding methods such as Shielded Metal Arc Welding (SMAW), Tungsten Inert Gas Welding (TIG), Plasma Transferred Arc Welding (PTA), laser welding, etc. This technique creates a strong metallurgical bond with the base material through a molten pool. This technique creates a strong metallurgical bond with the base material through a molten pool, which is different from the mechanical bonding of coatings or thermal spraying, and therefore stronger and more durable.
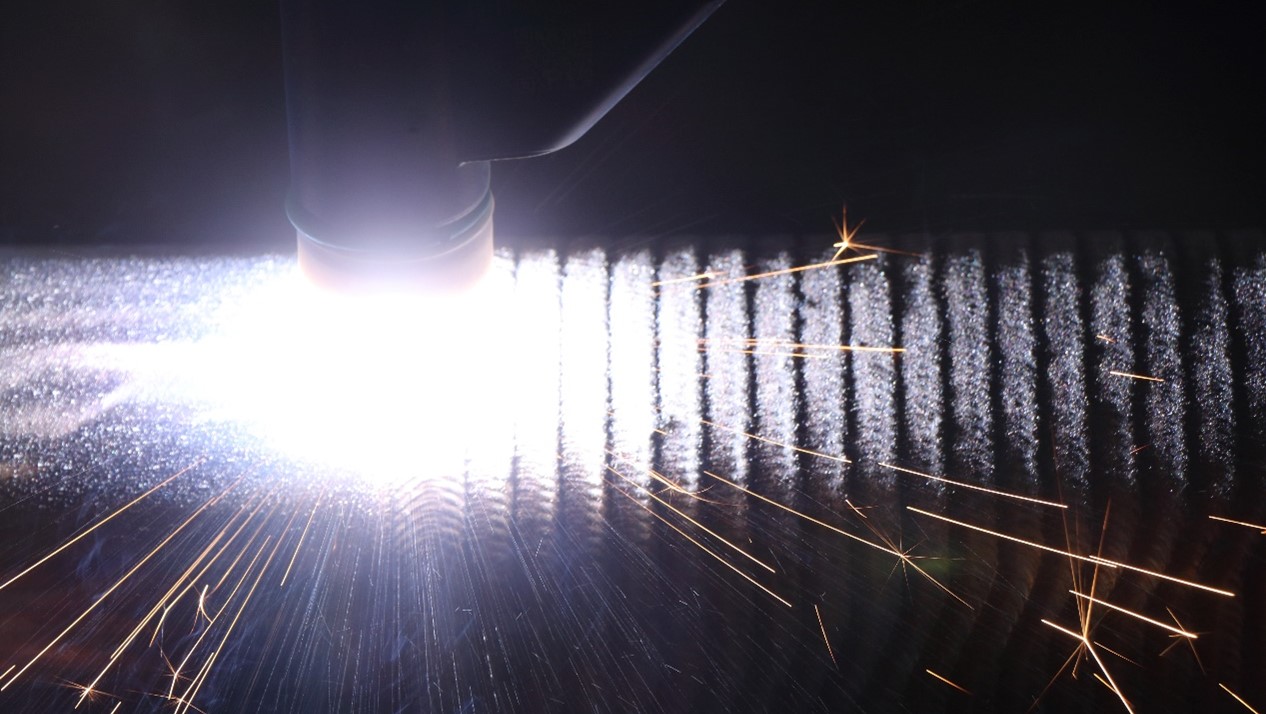
In engineering practice, weld overlay are commonly used to strengthen the surface of new parts and to repair old parts. For example, the working surface of the mold, the valve seat of the turbine, the vulnerable parts of the mining machinery, the lining of the chemical equipment, etc., are typical application scenarios of welding overlay.
The Role of Weld overlay
The main purpose of using weld overlay technology is to enhance the performance of the workpiece surface while saving costs. For high temperature, high pressure, corrosive or severely abrasive working environments, cladding can effectively enhance the surface durability of metallic materials. In addition, when mechanical components experience localized wear or corrosion, welded overlays can also be used to restore dimensions and performance, avoiding the need to replace the entire part.
The use of low-cost base materials and the overlay of high-performance alloys in critical areas is a cost-optimization strategy commonly used in industry today. By welding overlay layers, the use of expensive materials can be kept to the necessary areas, greatly reducing material waste.
Advantages of Welding Overlay
- Enhance the surface performance: through the selection of suitable welding consumables, the wear-resistant, corrosion-resistant, heat-resistant and other properties of the base material can be significantly enhanced;
- Extend the life of equipment: Surfacing the functional layer on the vulnerable parts can reduce the failure rate and extend the operating cycle of the equipment;
- Save material costs: the use of low-cost base material, only the key parts of the high-performance alloy deposition, reducing the overall material costs;
- Realize parts repair and reuse: wear or corrosion of parts for surfacing repair, to avoid scrapping the whole piece, significantly reducing maintenance costs;
- Applicable to a variety of metal substrates: can be used for carbon steel, stainless steel, alloy steel, nickel-based alloys and even some non-ferrous metals;
- Support automated welding: suitable for mass production or robotic welding operations, which can ensure the consistency and quality of welding.
Common Weld overlay Processes
The selection of weld overlay process is closely related to the type of base material, welding material, expected performance and construction environment. Common welding methods include:
• Shielded Metal Arc Welding (SMAW): suitable for small and medium-sized structures or repair sites, flexible but less efficient.
• Submerged arc welding: suitable for large area, thick layer surfacing, high degree of automation, fast deposition speed.
• Tungsten Inert Gas Welding (TIG): high precision melt pool control, suitable for thin-walled workpieces or precision welding.
• Metal Inert Gas Welding (MIG): high efficiency, easy to automate production, commonly used in manufacturing.
• Plasma Transferred Arc Welding (PTA) and laser welding: suitable for high-precision overlay welding or special metals, small heat-affected zone, small welding deformation.
During the welding process, the preheating temperature, interlayer temperature, welding sequence and cooling method should be reasonably selected according to the coefficient of thermal expansion of the base material and the alloy composition, in order to prevent defects such as cracks, porosity or biting edges.
Weld overlay material selection
Weld overlay welding material selection is the key, it directly determines the performance of the final surface layer performance. Material selection needs to be scientifically matched according to the use of the environment, for example:
- High-temperature oxidizing environment: choose nickel-based alloy;
- Strong corrosive media: choose cobalt-based alloys or high-alloy stainless steel;
- Strong impact wear environment: choose carbide or carbide enhanced welding consumables.
In order to control the dilution of the base material elements, usually using the transition layer + functional layer of the cladding method. The first layer as a dilution buffer, the second or third layer before the use of functional welding consumables to ensure stable performance.
Application of Weld Overlay
Welding overlay is widely used in the following industries and fields:
- Petrochemical industry: pressure vessels, pipelines, valves, heat exchangers, the inner wall of the anti-corrosion cladding;
- Power equipment: steam turbine valve seats, blades, high-temperature parts surfacing heat-resistant alloy layer;
- Mining machinery: crusher, bucket, bucket wheel, chute and other parts of the surfacing wear-resistant alloy;
- Nuclear industry: nuclear reactor wall surfacing stainless steel, enhance corrosion resistance;
- Mold manufacturing and repair: mold cavities, parting surface surfacing alloy layer for strengthening or size repair;
- Paper, ship, steel industry: all kinds of rollers, pulp pumps, agitators, screw rods and other key parts of the repair and strengthening.
The difference between weld overlay and thermal spraying
Although weld overlay and thermal spraying are both surface treatment technologies, there are obvious differences between the two in terms of the combination method, process characteristics and applicable occasions. Welded coverings are metallurgically bonded through high temperature welding, with layer thicknesses of several millimeters or more, and are suitable for high stress, high temperature, and high corrosion environments. Thermal spraying, on the other hand, usually has a lower bonding force and is suitable for applications requiring less thermal influence.
Weld Overlay Services By Shanghai Duomu
Shanghai Duomu Industry Co., Ltd. is a full-service welding shop that is ISO and CE certified and offers specialized welding, surface hardening and overlay services. For more information on how overlay welding can enhance the performance of your equipment, contact our team today.
Post time: Jul-17-2025