PTA welding the cutter ring in tunneling industry
The hob ring of a shield machine is an important cutting tool that is used for excavating rock tunnels. Its cutting principle relies on extrusion to break the rock, and it is particularly useful when excavating through loose strata that contain large particles or when the geological conditions of the tunnel are complex and changeable. In these situations, the hob ring is designed to be able to handle frequent staggering.
The hob ring is composed of a ring body with a hard alloy rolling ring on its outer periphery. To increase the strength and durability of the hob ring, protruding longitudinal ribs are added to both sides. However, due to the high friction and harsh usage environment, the contact surface of the hob ring is prone to wear and tear over time.
To address this issue, plasma surfacing can be applied to the hob ring. By using ceramic powder, spherical tungsten carbide, or nickel-based alloy powder, the hob ring can be strengthened and its overall lifespan can be significantly increased. Our customers have tested hob rings with plasma surfacing, and found that a thickness of 2mm is ideal for their needs.
In addition to improving the overall lifespan of the hob ring, plasma surfacing can also reduce costs by avoiding the need for frequent replacement of the hob ring. By using this technique, the hob ring can continue to be used for a longer period of time, resulting in cost savings for tunnel excavation projects.
Overall, the hob ring of a shield machine is a critical component for excavating rock tunnels, and plasma surfacing is an effective method for improving its durability and reducing costs. As such, it is a technique that is worth considering for any tunnel excavation project that involves the use of a hob ring.
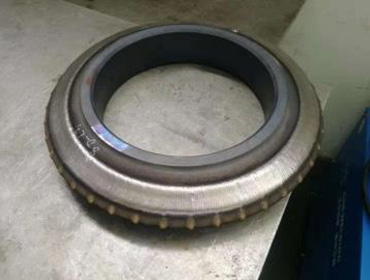
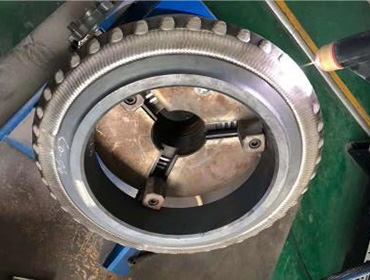
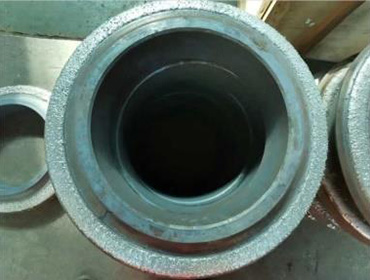
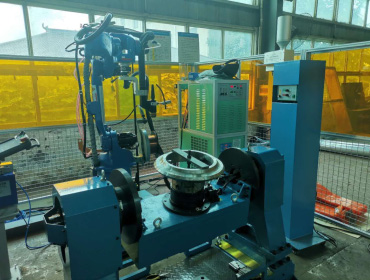
Video
Post time: Nov-17-2022