What is Tungsten Carbide Overlay Welding?
Tungsten Carbide Overlay Welding (TCOW) is a high hardness wear-resistant welding technique in which tungsten carbide particles (WC) and a metal bond are fused to the surface of a metal workpiece to form an extremely wear-resistant weld layer. This surface treatment significantly improves the wear resistance, erosion resistance and service life of the component.
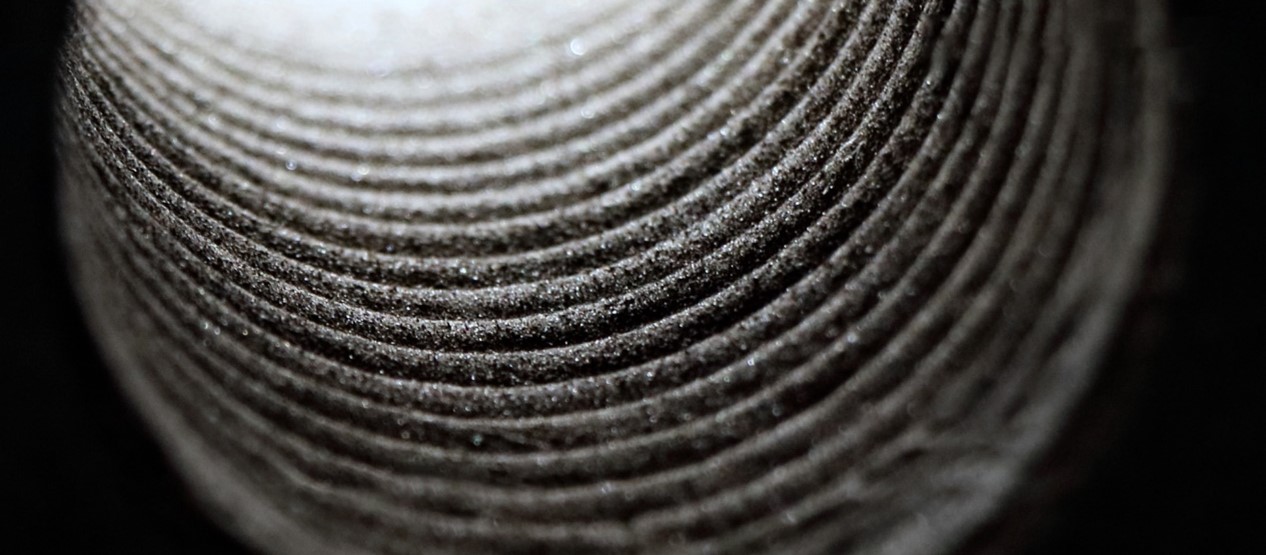
In mining, oil and gas, building materials, cement, electric power and other high wear industries, tungsten carbide overlay welding is widely used in the strengthening and repairing of various key equipment parts, which is one of the mainstream industrial-grade wear-resistant solutions.
Why choose tungsten carbide for overlay welding?
Tungsten carbide (WC) has excellent physical properties:
- Extremely high hardness: up to HRC 70~75, effectively resisting strong abrasive wear;
- High melting point: about 2870°C, high temperature resistance;
- Chemical stability: stable performance in most corrosive environments;
- Chemical stability: stable in most corrosive environments. Strong impact resistance: adapts to heavy loads and particle scouring.
These properties make it the first choice for high-strength wear-resistant welding materials.
Working Principle of Tungsten Carbide Overlay welding
Tungsten carbide overlay welding is a high-temperature welding heat source (such as plasma arc, laser, electric arc, etc.), the welding consumables containing WC particles are melted, and metallurgical bonding with the base metal occurs, forming a high hardness overlay welding layer with a certain thickness (generally 2~6mm).
The layer is usually composed of sintered WC particles and metal bonding agents such as iron, nickel, cobalt, etc. The particles are uniformly distributed in the weld channel, which has extremely strong wear resistance.
Several common types of tungsten carbide overlay welding methods
Depending on the application scenario and welding requirements, common tungsten carbide overlay welding processes include:
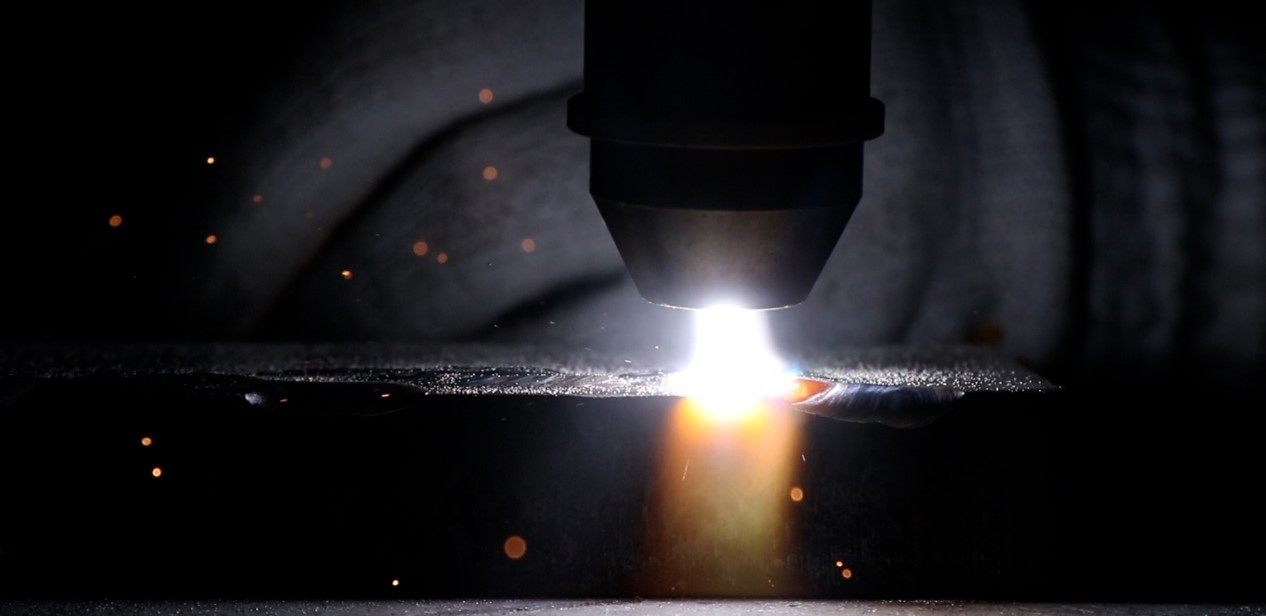
- Small heat affected zone, dense cladding layer;
- Suitable for small and medium-sized precision parts such as valves and seals.
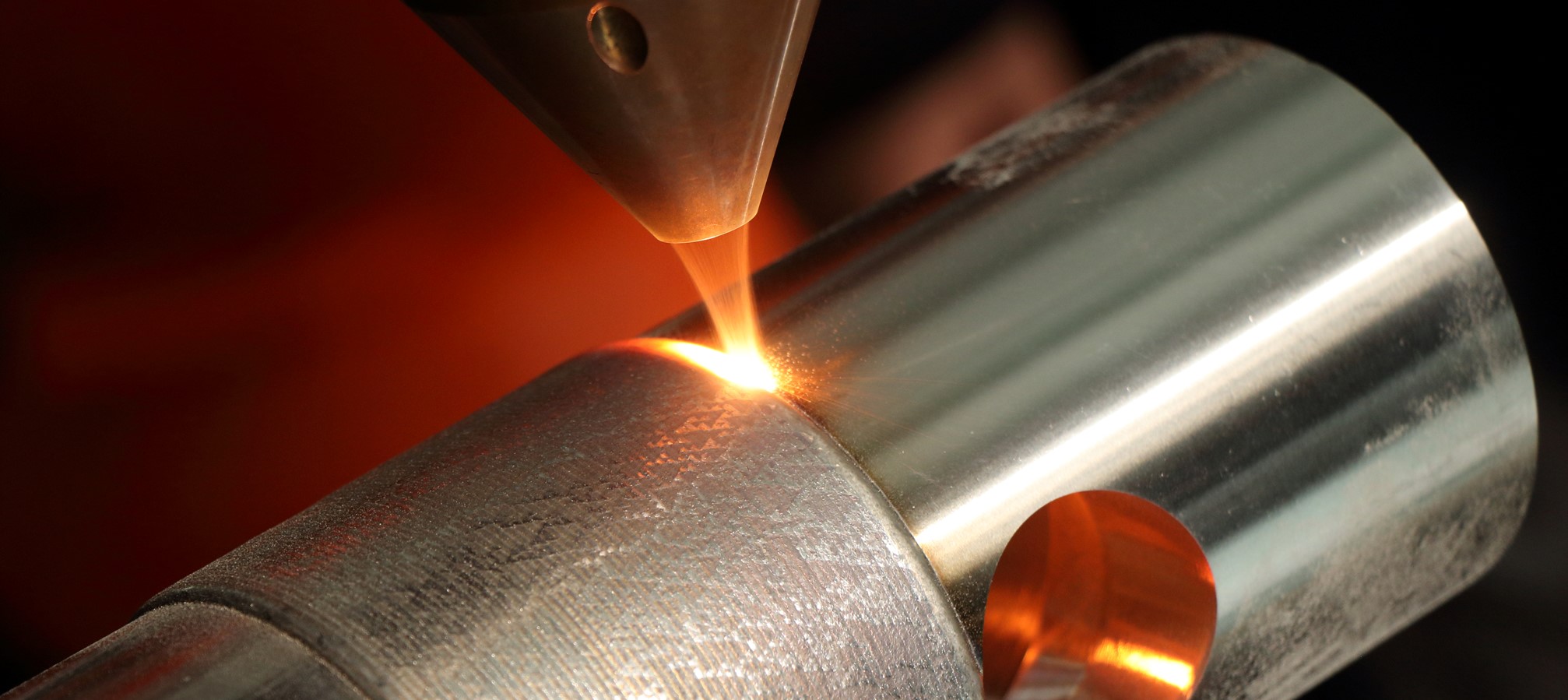
- Thinner welding layer, high bonding strength;
- Beautiful surface, suitable for high value-added workpiece surface enhancement.
3. Gas Metal Arc Welding/ Flux-Cored Arc Welding(GMAW/FCAW)
- Automated construction of large areas, high cost performance;
- Suitable for large mining equipment, grinding rolls and other heavy industrial parts.
Application Areas and Typical Parts
Tungsten carbide overlay welding has been widely used in several wear-resistant demand industries, including:
- Mining and extraction: buckets, conveyor scrapers, crusher hammerheads;
- Oil and gas: drill bits, valves, throttles;
- Cement and building materials: grinding rolls, grinding discs, air ducts, liners;
- Agricultural machinery: plow blade, plowing claw, crushing knife;
- Iron and steel metallurgy: rolls, molds, roller conveyor systems.
These parts are originally easy to wear, but through the WC overlay welding treatment, the service life can usually be increased by more than 3 to 10 times.
Core advantages of tungsten carbide overlay
1. extremely high wear resistance: higher hardness and longer life than conventional overlays
2. metallurgical bonding: strong bonding, spalling resistance;
3. high temperature and corrosion resistance: adapt to the harsh industrial working conditions;
4. Repairable overlay: significantly reduce equipment replacement costs;
5. Support customization: thickness of weld layer and type of particles can be adjusted according to requirements.
Technical considerations
• Control heat input to avoid WC particle burnout;
• Ensure uniform particle distribution to avoid “hole” or “segregation” in the weld channel;
• Transition layer design can be adopted to avoid cracks caused by hard layer directly welded on the mild steel substrate;
• Recommended thickness of the overlay layer: 2~6mm, excessive thickness may lead to the risk of stripping;
• Select iron, nickel or cobalt based bonding agent according to the working conditions.
Why choose tungsten carbide overlay welding?
Tungsten Carbide overlay welding not only significantly improves the surface properties of workpieces, but is also an economical, efficient and sustainable solution for industrial surface treatment. For working conditions that face abrasive wear and corrosive washout all year round, WC overlay welding is a reliable choice for protecting core components, extending service life, and reducing the frequency of repairs.
If you are looking for high-performance wear-resistant welding technology, tungsten carbide overlay welding is a solution worth prioritizing.
Post time: Jul-09-2025